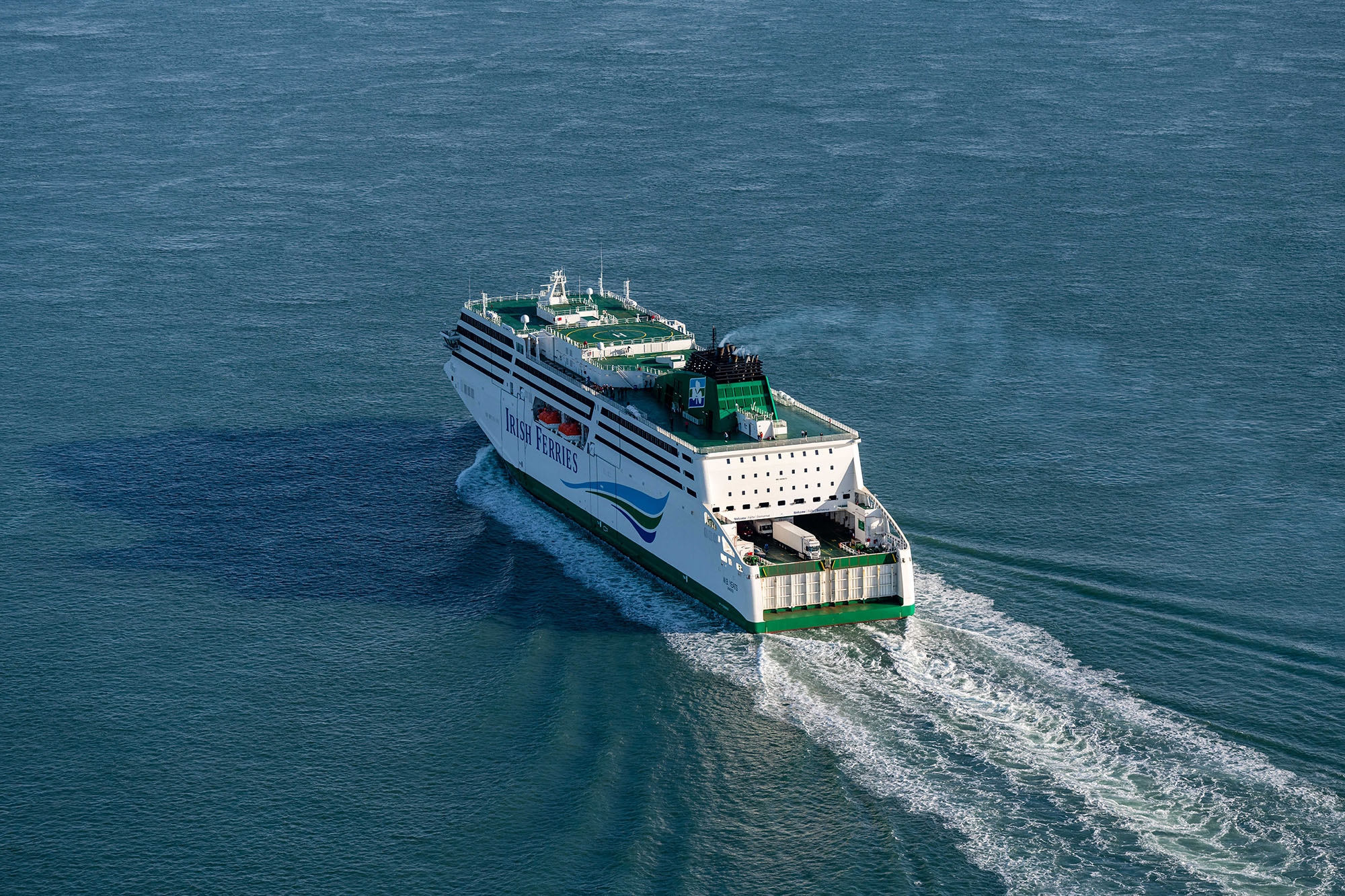
ICG Strategy and the Environment
A commitment to safeguarding the environment and operating in a sustainable manner is a key deliverable of ICG strategy. A continuous focus on its cost base drives improvement in operational efficiency resulting in lower inputs and wastage levels, and maximises asset lives all of which ultimately improves our environmental performance.
In recognising that small changes can deliver cumulatively large efficiencies over time ICG has developed a groupwide environmental framework the objective of which is to facilitate the continuous improvement of the environmental effects of the Group’s activities in a unified and structured manner.
On a wider societal level ICG plays a pivotal role in Ireland’s traded goods logistical chain while Irish Ferries’ passenger services contribute significantly to the tourism industries of Ireland, the United Kingdom and France.
The Group’s principal activity is the operation of ships and provision of related services. While transport by sea is one of the most efficient modes of transport, as measured by cargo tonnes per kilometre, these activities still have an unavoidable impact on the environment. This report provides a summary of the principal initiatives implemented by the Group to minimise this impact over four key areas; vessel design, fleet operation, on board hotel activities; and terminal activities.
Vessel Design
The Group operates a total fleet of four ferries (three owned, one chartered-in), one fast craft and six container vessels (four owned, 2 chartered-in). The Group commissioned all three owned ferries and the chartered-in ferry is due to be replaced by a further commissioned newly built ferry. The efficiency characteristics of our fleet commence at the design phase with incremental improvements made over the life of a vessel. Projects completed or commissioned during 2019 are described below.
Construction Design
When commissioning new vessels the Group is committed to the application of innovative design features intended to minimise environmental impact. By law, all new ships from 2013 onwards require an Energy Efficiency Design Index (EEDI) whereby new ship designs must meet an efficiency reference level. The W.B. Yeats has a required EEDI of 18.5g of CO2 per tonne-mile. The new cruise ferry under construction at a contract price of €165.2 million will fall under phase two of EEDI as construction takes place from 2020, meaning its required efficiency will be a ten percent improvement on that designated for the W.B. Yeats.
Ballast Water Management
The intake and discharge of ballast water (sea water) is an integral part of vessel stability management, though poor management of ballast water systems can damage local biodiversity through transference of non-native marine species.
The Group has implemented a Ballast Water and Sediments Management Plan across all its fleet for correct management of ballast water to help prevent the spread of non-native marine species by transference. Our newest vessel W.B. Yeats has already been designed with ballast water treatment systems, while in 2020, the Group will complete feasibility studies and set out investment proposals for ballast water treatment equipment across the remaining fleet from 2021. Pending completion of this upgrade project the operating protocol is that all ballast water is loaded and discharged at the same location so as to avoid species transfer.
In addition to reducing the risk of transference, this project will also improve fuel efficiencies through avoiding excess carrying of ballast waters.
Paint
A key factor that affects vessel performance apart from the optimal engineered design of the hull is the maintained condition of the hull itself. Central to this is maintaining a smooth underwater hull surface to reduce resistance when moving through the water. Once in service a vessel’s hull is exposed to corrosion and fouling, which studies indicate can adversely affect fuel consumption by up to four percent. To maintain maximum efficiency as part of ongoing maintenance ICG vessels utilise modern silicon based non-toxic paints which avoid the release of harmful agents into the sea. These assist in preventing corrosion thereby ensuring maximum hull life, reducing fouling between drydockings and lowers the risk of damage to local biodiversity.
Propeller Caps
The W.B. Yeats was delivered fitted with the latest energy efficient propeller blades. These incorporated rotating propeller caps which decrease propeller resistance and increase thrust. This increases overall propulsion efficiency and reduces fuel consumption. Having assessed this technology, a full set of similar propeller blades were retro-fitted to the Ulysses during 2019.
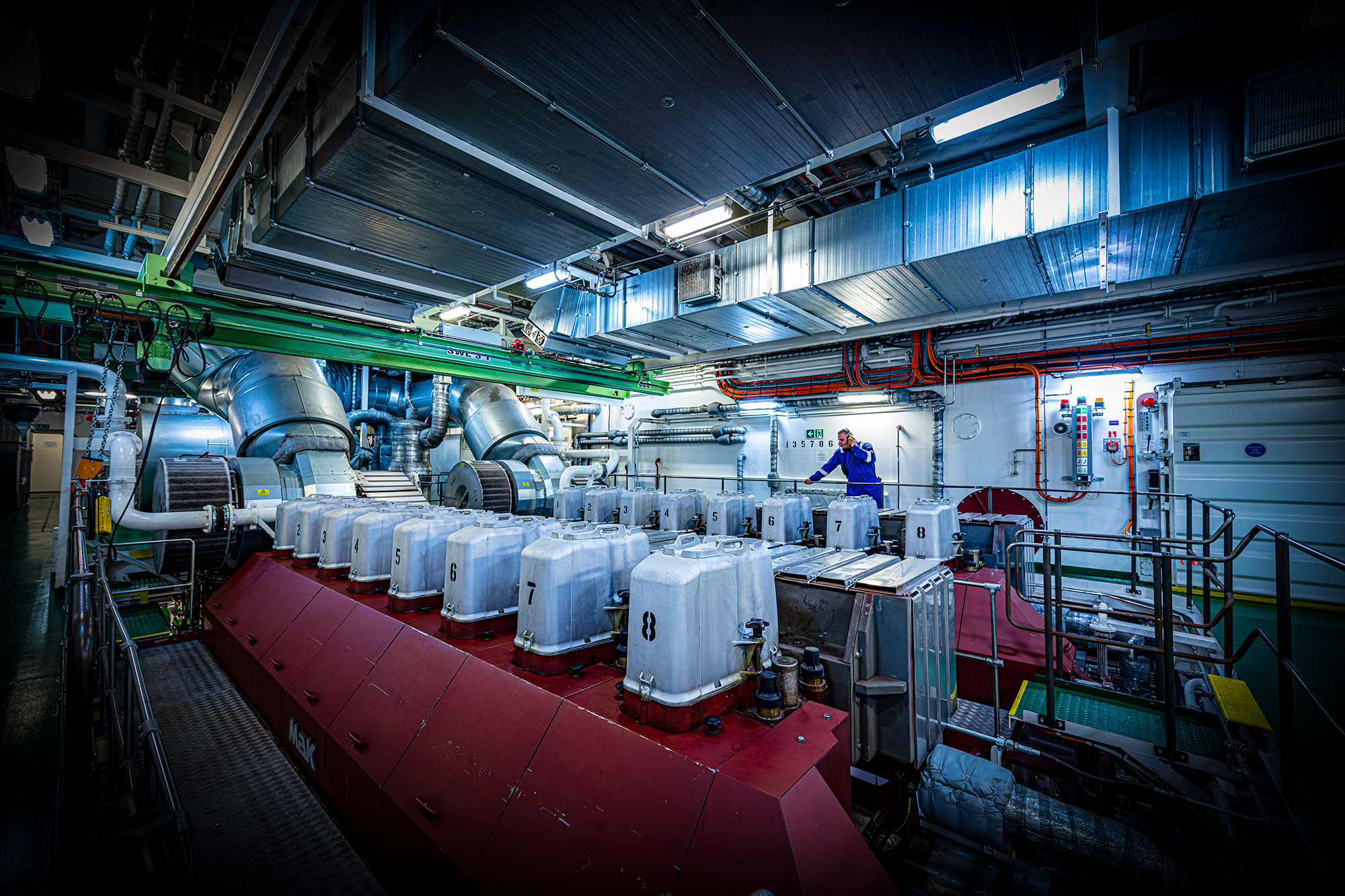
Strategy in Action
Exhaust Gas Cleaning Systems
The International Maritime Organisation (IMO), a UN sponsored body adopted by the European Union, has issued new fuel regulations (IMO 2020) which are effective for all shipping operators effective from 1 January 2020. IMO 2020 requires all our vessels operating outside of sulphur emission control areas (SECA) to reduce sulphur emissions equivalent to consuming 0.5% sulphur content fuel oils compared to the previous permitted 1%. Over the last decade these permissible levels have been decreased in stages from 3.5% to the current 0.5% and 0.1% when operating in SECA.
The fastcraft Dublin Swift consumes marine gas oil which has a delivered sulphur content of 0.1% thus already in compliance and bettering the new regulatory requirement in its geographic area of operation.
On its owned and operated fleet, the Group has taken the decision to install Exhaust Gas Cleaning Systems (EGCS) to comply with these latest requirements. The cruise ferry W.B. Yeats which commenced sailing in the fleet in 2019 was delivered an EGCS. This ensured that this vessel complied with the 0.5% sulphur cap on marine fuels in advance of the 1 January 2020 deadline. The cruise ferries Isle of Inishmore and Ulysses and the owned container vessels operated by the Group will each have EGCS installed during 2020 and pending completion of those installations will consume heavy fuel oils with a delivered sulphur content of 0.5%. In opting for EGCS the Group performed a thorough assessment of alternatives, including a conversion to LNG fuels and found the EGCS option to be the safest and most environmentally friendly solution. In addition to managing sulphur emissions studies have shown that EGCS can remove 60-90% of particulate matter (PM or black carbon), including a portion of small and ultrafine PM, resulting in fewer particles released in the atmosphere compared to consuming 0.5% fuel oils or marine gas oil.
The experience to date with the W.B. Yeats is that achieved sulphur emissions are below permitted levels with on-board emission alarm levels set lower than the maximum permissible.
Total Group investment for supply and installation of EGCS is estimated at approximately €25 million. In addition to improving ICG’s environmental performance this investment allows the Group to consume lower cost fuel oils and in the event that a vessel may become surplus to operational requirement allows for greater geographical operational ability increasing the marketability of the vessel to a third party.
Fleet Operations
Ship Energy Efficiency Management Plan
Under IMO requirements each vessel has developed a Ship Energy Efficiency Management Plan (SEEMP). The SEEMP contains a multitude of measures intended to improve the energy and environmental efficiency of a ship in a cost-effective manner. While all plans are vessel-specific, they each follow a Plan-Do-Check-Act iterative cycle for improvement.
Key SEEMP measures, all of which improve the fleet environmental performance include;
- Fuel efficiency maximisation
- Speed optimisation for sea conditions
- Minimisation of hull resistance through sailing parameter optimisation
- Engine performance management
- Boiler performance management
- Bunker management
Efficiency in operation
ICG is developing a program to increase operational efficiency awareness across its fleet through recording the operational profile for each voyage conducted in service. Due to be introduced in 2020, each scheduled voyage carried out with plant safely reduced below the standard operational profile due to efficient port operations, navigational routing, trim of vessel, good weather, speed management or a combination of the above while maintaining schedule will be classed as a ‘clean voyage’. It is proposed that clean voyages will be recorded throughout the year and associated reduction in CO2 emissions estimated and used to benchmark against annually to ensure continuous improvement.
Additionally, during 2019 the Group has commenced reporting under the EU Monitoring, Reporting and Verification guidelines (MRV) which requires ships to monitor and report CO2 emissions, fuel consumption, transport work and average energy efficiency each year. In time this data will provide a benchmark to track improvement.
Refrigeration and Air Conditioning Emissions
All our vessels have refrigeration and air conditioning systems which utilise hydrofluorocarbons gasses (HFCs) which are known to cause ozone damage if leaked into the atmosphere. All owned vessels are fully compliant with the EU ‘F-gas’ Regulation restricting the usage of certain HFCs and imposing bans on certain other HFCs with the highest global warming potential. Leakages of all refrigerant gas on board vessels are to be recorded in 2020 with the intention of implementing an action plan to work towards a zero-leak environment by 2022.
Waste
The disposal of waste at sea is strictly prohibited by regulation and all vessels have a waste disposal plan. All vessels use oil recovery systems to recover spent oils which are then sent for recycling to processors with regulatory approvals. All other vessel waste is segregated where possible and sent for recycling at approved facilities.
Under the most recent biennial reporting to the Irish Central Statistics Office, the Group has recorded reductions in its wastage in 2018 over 2016 with an overall reduction of approximately 1,100 tonnes. This represents a 30% reduction in waste sludge and oil water and a 68% reduction achieved across other waste types, including packaging, paper and electronic waste.
Hotel and Catering Activities
Welcoming over 1.5 million guests aboard our cruise and passenger ferries annually our on-board hospitality services contribute significantly to our environmental performance. We are continually seeking ways to improve our performance in the following key areas;
Responsible sourcing
Where possible we seek to increase the use of local suppliers and showcase local produce supporting artisan producers. Typical examples include our fish supplier, a large family-owned fishmonger based in the fishing town of Howth in North County Dublin who supply locally sourced seafood utilising sustainable fishing methods. We source all of our fruit and vegetables through Irish distributors who guarantee to deliver the freshest produce from farms all around the Country. When in season Irish produce will always be selected before imported goods. All our beef is Irish produced and our Irish dairy, cheddar cheese and eggs are origin green certified. Our breakfast meats are sourced in Kilkenny and Cork. We are a strong promoter of Irish beverages not only the popular brands but also smaller producers of craft beers and spirits. In line with the demands of our guests we now offer a wide variety of plant based food and drink options in all our cafes and restaurants with plans to increase this range of offering in 2020. Our coffees are provided by a Dublin based roaster, using the world’s first purpose-built carbon neutral roastery in Dublin and coffees and teas served on board are fair trade certified. Our supply chain seeks to minimise the number of deliveries to our vessels through the use of containerised provisioning.
Single use plastics
We committed during 2019 to remove single use plastics and other non-compostable consumables from our restaurants. We are well on the way to achieving this goal during 2020 where all food packaging and coffee cups will be produced from compostable materials. We have also introduced an awareness programme for our guests through the use of our turtle logo.
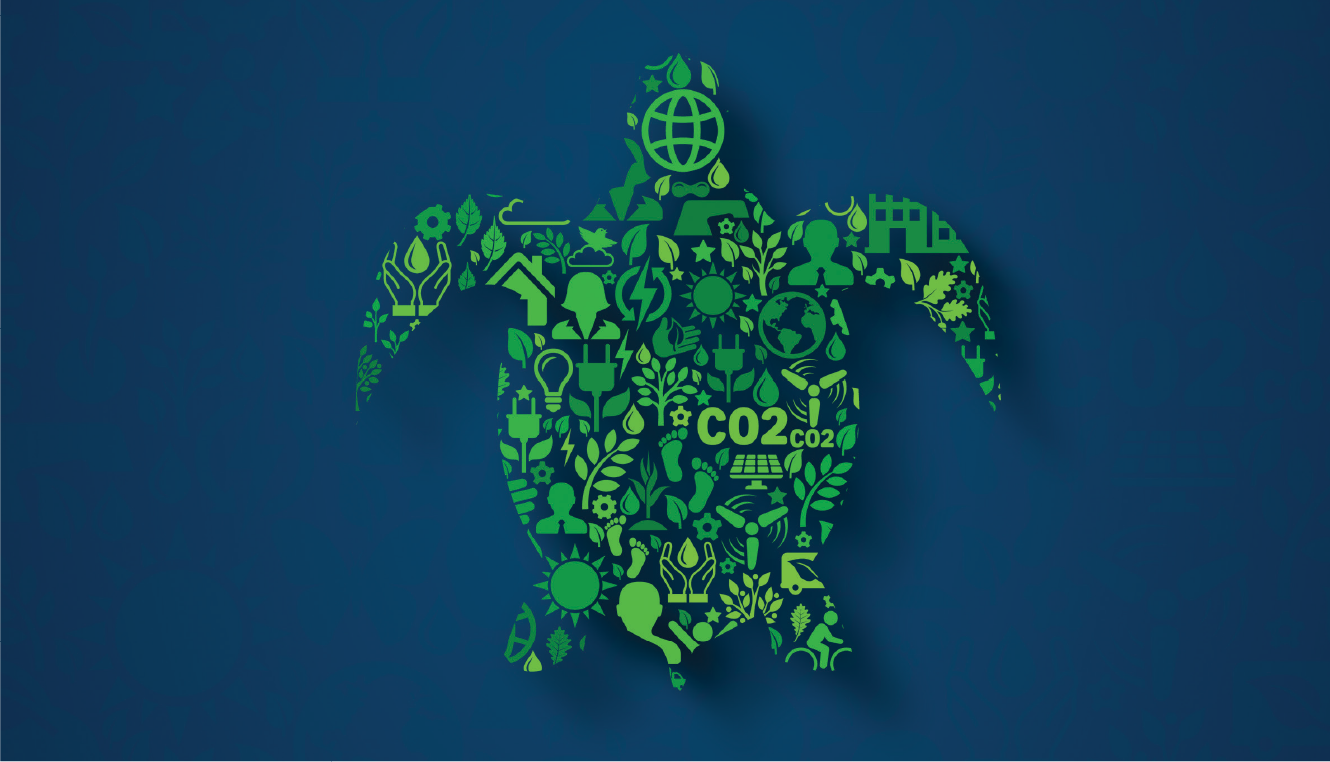
Water conservation
All water used on board our vessels is of potable standard. As this is both a scarce resource and an increasing cost ICG seeks to reduce consumption on-board vessels through water saving devices such as flow controllers without interrupting our guests’ comfort. Water conservation is covered in environmental awareness information made available to our crews.
Related to water conservation is waste water treatment systems. All our vessels have foul water treatment systems which meet strict regulatory requirements at least equivalent to land based systems before discharge into open seas away from coastal areas.
Cleaning and hygiene
With up to two million laundry items per annum ICG requires that its laundry service provider should be as environmentally conscious as ICG. Our laundry contract has been awarded to one of Ireland’s leading laundries whom ICG is satisfied is accredited as complying with the highest environmental standard with a commitment to minimum use of harmful detergents and a recycling program.
In our cabin accommodation we use ozone sanitary systems which has high oxidant power to eliminate odours and harmful bacteria while significantly reducing the use of chemical products.
Other on-board initiatives
Equally important to the significant initiatives above are the myriad of smaller changes that are constantly being implemented an example being a switch to coreless tissue dispensers removing over 300,000 cardboard cores from our previous waste output.
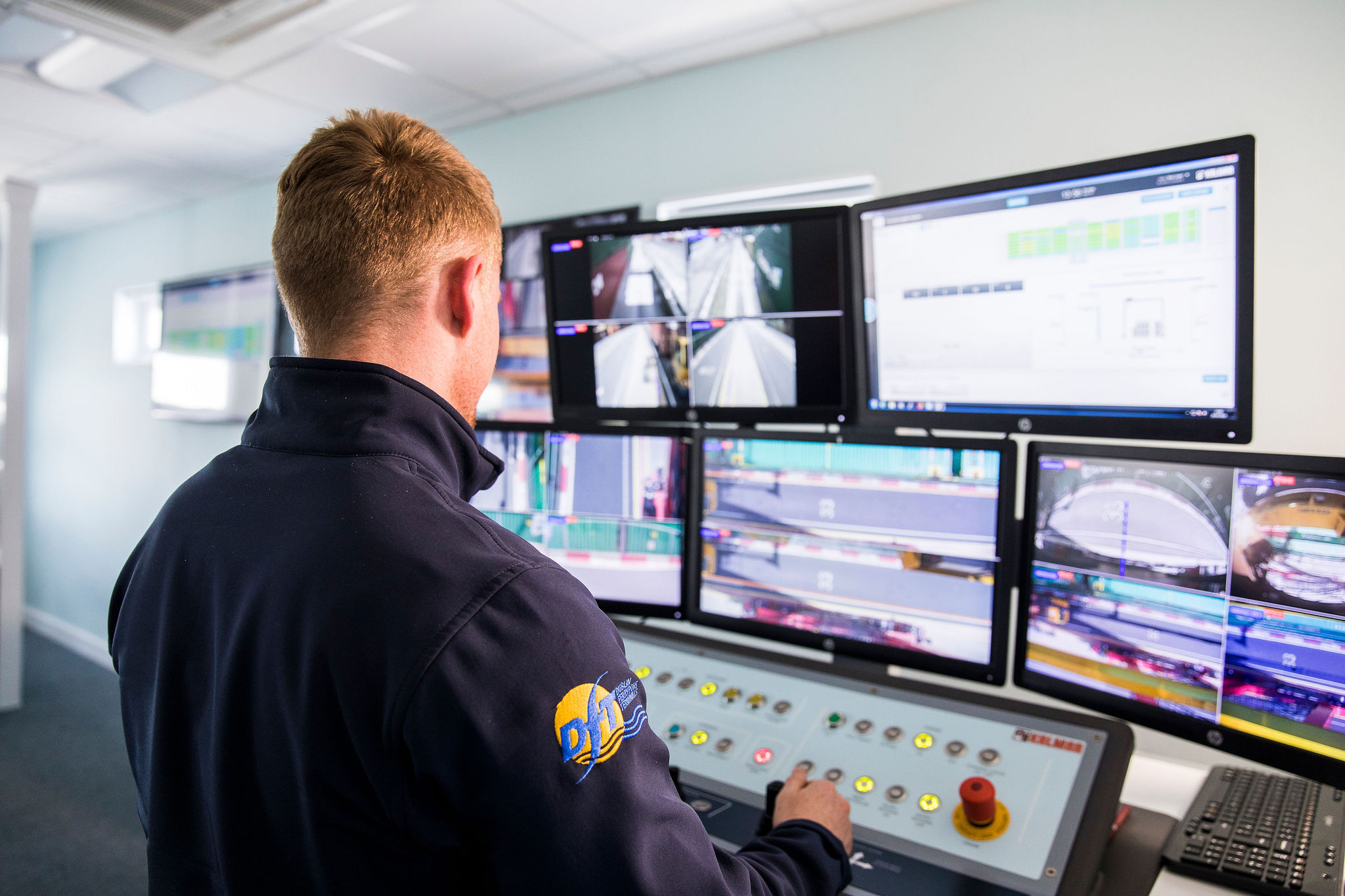
Terminal Operations
The Group’s container terminals at Dublin and Belfast utilise energy in the form of direct consumption of fossil fuels and electricity generating exhaust emissions. The nature of operations is that terminals also generate road traffic and certain levels of noise. ICG has a number of projects in place to improve environmental performance at its container facilities.
Strategy in Action
Increased electrification of heavy plant
The two most recent commissioned mobile gantries (RTGs) at our Dublin Ferry Port Terminal represented a change to electrical power from previous diesel combustion. The advantages are greater efficiency due to zero idling, lower emissions and noise levels. Currently 20% of our RTG fleet is electrically powered which is expected to increase to 33% following delivery of further units during 2020. The three ship to shore cranes are already electrically powered.
At our Belfast terminal our landlord partner Belfast Harbour Commissioners have commenced an investment program whereby they are also changing the plant which we operate from diesel units to electrical units.
Increased Automation
In conjunction with our investment in new RTGs at Dublin we commissioned our first automated container stack during 2019. This has improved container handling efficiency significantly, while further increasing the level of occupational safety in the port. We are currently commissioning a second automated stack in conjunction with the delivery of the two additional RTGs scheduled for delivery in 2020.
The modernisation of the Belfast terminal by our landlord will also incorporate this technology.
Transport Management System
A new transport management system having been trialled during 2019 is scheduled to be operational during 2020. This will facilitate reduced waiting times and idling time on the part of our sub-contracted hauliers while also improving aspects of operational safety within our terminals.
Offices
While our office locations are the least environmentally impactful aspect of ICG operations we have adopted an environmental plan to generate environmental awareness of the impact of our administrative activities. ICG has a waste management plan in place for its offices and ports. With the help of staff, suppliers and visitors we aim to prevent waste and discontinue the use of environmentally damaging products as a primary goal. Having moved to energy efficient lighting during 2018, the 2019 initiative was to optimise the uncontaminated segregation of compostable, recyclable and general waste to enable its waste partners to effectively process waste and to replace all single use plastics with compostable alternatives in office canteens and recreation areas.
Social and Governance
Community and Wellness
The Group continues to take an active interest in the communities within which it operates. Each separate business unit assists in local initiatives through sponsorship and organised events. ICG recognises the important role played by charities and community organisations within its communities and we are happy to help these organisations achieve their goals. Irish Ferries has been a main sponsor of the Dublin St. Patrick’s Day festival. The Group is also happy to support its employees with charitable endeavours of their own. Irish Ferries works with the Irish Whale and Dolphin group by reporting information on sightings and facilitating surveys to assist in the conservation and understanding of cetaceans in the Irish Sea.
Staff
The general health and wellbeing of employees and customers is of utmost importance to the Group. ICG participates in the ‘Cycle to Work’ scheme and provides an on-site gym facility at the Group head office, available to all staff.
ICG is an equal opportunities employer and while the industry is heavily male represented, the Group believes diversity is necessary to drive innovation, make better decisions and maintain a talented workforce. As of 31 December 2019, 33% of the Group’s employees were female. Whilst this is not representative of the population at large it is characteristic of the sector in which we operate. Cognisant of the need to better reflect societal composition, the Group has put in place an initiative to seek out larger numbers of female candidates when conducting recruitment.
Safeguard of vulnerable persons
ICG imposes strict obligations on the entity responsible for the technical and crewing management onboard its ships, the applicable contractors it employs and its management teams to comply with all applicable laws, including those relating to labour and employment practices. ICG requires a due diligence process to be conducted prior to the appointment of a contractor together with in-contract reviews.
Within its day to day operations ICG has in place a range of measures to help ensure modern slavery and human trafficking are not taking place in its business or its supply chains. Measures adopted include;
- Provision of guidance to employees to support immigration and border agency initiatives to reduce human trafficking, which augments general observation for unusual behaviour in our ports and onboard our vessels. Awareness of this issue is promulgated across all Group businesses.
- Working with other companies and organisations to share knowledge, learning and best practise and co-operating with a series of law-enforcement projects that help to combat human trafficking and modern slavery.
- Regular updates to management and committees on modern slavery so that directors and key individuals understand their role and accountability for the prevention of modern slavery occurring in our businesses and supply chains.
- Actively monitoring its initiatives in preventing modern slavery and human trafficking by reference to reports and alerts from staff, the public and communication with law-enforcement agencies.
Safety
The promotion and maintenance of a strong safety culture across all activities is a principle strategy of ICG, to not only ensure the safety, security and well-being of our people and passengers, but also so that all stakeholders reap the competitive rewards that come from giving safety top priority.
The Group’s operations span a wide range of activities, both ashore and afloat. It is a matter of high priority that all our activities are conducted in a manner that ensures the safety and security of all our people, and all those who travel on board our ships or visit our terminals. The bedrock of ICG’s safety performance is our people. We place strategic emphasis on ensuring all those who work within the Group’s sphere of operations are competent, provided with a high level of safety and quality training and information, and are encouraged to engage with the Group’s continuous improvement philosophy.
Compliance with policy and procedures, both ashore and afloat, is monitored by regular and detailed audits. Audits are conducted by trained and experienced auditors in an open yet focused manner that drives compliance and improvement. Senior management monitor safety and audit performance across the Group, identifying and addressing safety trends and opportunities for improvement where they may arise.
In addition to the Group’s own internal verification procedures, our activities are subject to regular routine inspection by national and international statutory bodies. They, like us, set high standards to ensure the safety and well-being of all personnel, passengers and cargoes; standards that we as a Group are ready to meet and exceed.
Ashore: As a minimum, all the Group’s activities are conducted in strict compliance with the various statutory health and safety standards and international maritime regulations that apply. In accordance with the Safety, Health and Welfare at Work Act 2005 and its equivalents in other jurisdictions, the Group has in place safety policies and safety statements that guide our activities. We have in place a system of hazard identification and risk assessment that ensures all necessary steps are taken to minimise and mitigate safety risks. Agreed procedures ensure that activities and operations are conducted in a consistent and safe manner. By fostering a culture of employee competence and participation we empower our employees to continuously improve the efficiency and safety of our activities, so contributing to a safe environment for all.
At Sea: ICG ensures that all its ships are designed, operated and maintained in compliance with the International Convention for the Safety of Life at Sea (SOLAS). This Convention is administered by the UN’s International Maritime Organisation and is subject to continuous international review and updating, ensuring ship safety standards keep pace with societal expectations and technological advances.
The safety and security of ship’s crews, passengers and cargoes is critical to our business, and is always the primary consideration. ICG ships are certified in accordance with the International Safety Management (ISM) Code, the international standard for the safe management and operation of ships and for pollution prevention.
ICG also operates in full compliance with the International Ship and Port Facility Security (ISPS) Code on board all ships and at all locations. The on-board management of the Irish Ferries operated vessels was performed by Matrix Ship Management Limited, Cyprus, on behalf of ICG.
While the focus is on accident prevention where incidents do occur, effective internal and external reporting and investigation systems are employed to identify the cause of such incidents and put in place actions to prevent recurrence. Due to the highly regulated environment in which we operate, incidents may be subject to external investigation by the appropriate regulatory authority. The Group will always work with the authorities toward a successful and worthwhile investigation outcome.
Lost Time Injury Frequency (LTIF) is a metric used to measure workplace safety. LTIF measures the number of workplace incidents causing an employee to miss the following day’s work per million hours worked. The Group’s LTIF rate for 2019 was 1.6 (2018: 1.6).